Oh my god, we’re going to talk about robotics! Finally, an article where we can talk about technological innovation, agricultural (r)evolution – because the parenthesis around the “r” is super important – and the third way of agriculture! Yippee! So if this article doesn’t make the buzz, I don’t understand anything anymore!
Too bad, spoiler alert …
The robotics sector continues to develop strongly in the agricultural context. The number of robots on offer continues to grow, yet the number of units sold remains low. As with any emerging sector, the robotics industry is still searching for its place. The French government seems to welcome the development of agricultural robotics and is still considering injecting public money into the sector. As part of the “Sustainable agricultural systems and equipment contributing to the ecological transition” (SADEA) acceleration strategy, and the future investment programme (PIA4) backed by France 2030, the French government has asked the RobAgri association – the robotics association in France, which has nearly 80 members – to draw up a Grand Challenge dedicated to agricultural robotics. This challenge is an opportunity for the sector to build synergies between robotics and agro-ecology.
This dossier on robotics is also an opportunity to promote all the knowledge that is beginning to be capitalised on the directory of digital tools for agriculture. In addition to serving as a collaborative watch, this platform is now used to take a step back from the digital tools in place and to identify trends.
As usual, for readers of the blog, this article is based on video interviews with players in the sector (whose names you will find at the end of the article) whom I thank for the time they were able to give me. Several articles, reports and seminars have enabled me to complete the feedback from the interviews.
You will see from the interviewees that there are relatively few robot manufacturers. It’s not for lack of trying…
Enjoy your reading!

Robotics
Important preamble
It must be admitted that it is not easy to find one’s way in the agricultural robotics ecosystem. The sector includes many different players (just take a look at figures 1 and 2, which are certainly not exhaustive) and there is an impression of individualism where each player seems to go off in his own direction with his own budget. The adoption of robots is in any case difficult to grasp, follow and understand because we do not really know where we stand. It must be said that manufacturers and roboticists do not give us much information. We can understand that there are industrial and competitive issues, but the fact that we don’t have a clear overview of what exists in the field of robotics doesn’t allow agricultural players to find their way in this complex ecosystem. This is a limitation that we are trying to overcome with our directory of digital tools for agriculture
All the figures you will find in this file are related to the robotics tools presented in the directory of digital tools for farmers. These figures will evolve over time according to the consolidation of the databases (the information is not always of good quality – due to referencing or lack of information from suppliers), the addition of tools and/or feedback from users and suppliers. This platform is participatory and collaborative. Everyone can contribute by adding new tools, proposing modifications to existing tools or commenting and rating the tools on the platform.
The robots presented here are used in agricultural contexts (plant and animal). I only present here robots on the ground or close to the ground. Aerial robots – mainly drones – are not considered here.
Please keep this in mind while reading this work!
Overview of agricultural robotics by sector
A few years ago, one could have said that the robotics sector was almost non-existent in the agricultural sector. The interest was rather focused on the development of digital tools (sensors, decision support tools, management software…). The tide now seems to have turned and, if the general impression of digital tools is that of a rather slow evolution and perhaps running out of steam, robots have been widely developed. The panorama of robotic systems is extremely broad (see figures 1 and 2)

Figure 1: Overview of robots in animal production. Source: Directory of digital tools for farmers Translation by turning clockwise from the top : Alimentation (Feeding), Nettoyage (Cleaning), Paillage (Mulching), Repousse-fourrage (Forage Movement), Santé et Bien-Etre (Health and Wellness), Traite (Milking)

Figure 2. Overview of ground robots in crop production. Source: Directory of digital tools for farmers Translation by turning clockwise from the top : Récolte (Harvesting), Semis (Sowing), Stockage (Storage), Surveillance Inspection (Monitoring-Inspection), Taille (Pruning), Tonte (Mowing), Travail du sol (Tillage), Triage (Sorting), Déplacement objets ou personnes (Moving objects or people), Désherbage (Weeding), Echantillonnage (Sampling), Eclaircissage (Thinning), Fertilisation (Fertilisation), Eclaircissage (Leaf removal), Epamprage (Shoot thinning), Itinéraire cultural (Crop itinerary), Phénotypage (Phenotyping), Pollinisation (Pollination), Protection des cultures (Crop protection)
Robots are designated all over the world (Figure 3 – there is certainly a bias in the referencing of robots in view of my French and westernised vision of the matter). And the actors are varied (I refer you to a beginning of a mapping of roboticists in Europe made by UnilaSalle students in 2022 – UnilaSalle is an agronomic university in France).
Although the definition of robotic systems is still debated for reasons of mobility, degree of autonomy, learning capacity, extent of decision-making or the ability to pre-programme the robot, we have considered robots here in a fairly broad sense. The robots represented here are mechatronic systems capable of performing tasks in a fairly autonomous way (we will see that complete autonomy does not really exist) under human supervision (in collaboration or not) for applications in plant and animal contexts.

Figure 3: Number of robot models referenced by country on the platform. Not to be confused with the number of robots sold (data not available). Source: Directory of digital tools for farmers Translation of countries from left to right : France (France), Allemagne (Spain), Etats-Unis (United States), Pays-Bas (Netherlands), Angleterre (England), Canada (Canada), Europe (Europe), Suède (Sweden), Australie (Australia), Israël (Israel), Autriche (Austria), Belgique (Belgium), Japon (Japan), Espagne (Spain), Suisse (Switzerland), Chine (China), Finlande (Finland), Norvège (Norway), Pologne (Poland), Irlande (Ireland), Italie (Italy), Ukraine (Ukraine)
A focus on animal production
It is difficult to take an interest in the robotics sector as a whole, as current robot sales are so unbalanced between crop and animal production. In the animal context, the economic model seems rather clear, proven and seems to work. It is an important investment for the farmer, but a good part of them will acculturate to it rather well and will take advantage of the flexibility, agility and comfort offered by the robotic units. In livestock farming, robotic systems are well established because they are units that do not incorporate much intelligence (milking robots, feeding robots, mulching robots, manure scrapers, etc.) and that mainly allow farmers to reduce the drudgery of their work and to reorganise their time. Family-run livestock farms are also tending to be interested in milking robots to make it easier to combine family life and work.
Milking robots are the best-selling autonomous systems (the Observatory of Digital Agricultural Practices gives the figure of more than 10,000 units sold in 2018 – Lachia, 2018). They can be seen as a support service or a herd management service in the sense that there is a follow-up of milk control and genetic expectations. Some farmers will prefer to go back to the drawing board after trying these robots for a variety of good and bad reasons, but the overall picture from users seems positive with an innovation that seems to be living its life. The references are starting to be historical and solid. The optimal number of cows and the milk production required to make the installation of the robot profitable are known, and the animal industry has some experience of how to install these robots.
Surprisingly for some, milking robots do not meet the challenges of economy of scale. The idea of ever larger and simpler farms to improve performance with robotic milking systems in all directions is in fact quite far from reality. The optimal number of cows per milking robot would be around 60-70 cows (small dairy farms would therefore tend to increase their herd to reach this number if they invested in a milking robot) but there would be a herd threshold beyond which milking robots would no longer be of interest (even if the number of milking robots was multiplied) because they would impose too great a change in organisation (in terms of human ressources management of employees and organisation of teams for shifts and weekends). Gigantic dairy farms are not so robotised (for milking at least) and maintain fairly classic rotolactor systems (a kind of revolving carousel) which, on the contrary, are adapted to economies of scale (many more cows can be put in them). The main observation is therefore the non-linearity between the size of the farms and the number of milking robots used.
The distribution networks are increasingly structured with different sales strategies depending on the territory, alternating messages between production costs, profitability of the installation, or milk quality, and offering pricing services based on the number of litres of milk milked or the number of connections (Martin et al., 2020, 2021). The current organisation is still mainly based on a milking robot in a building with cows in stalls. It is hoped that the business models will evolve to accommodate greening models with predominantly grazing and robotic systems outside the barn.
In livestock farming, robots are much better established in the beef (and particularly dairy) sector than in other sectors (Figure 5). The beef sector is indeed more widely developed in terms of numbers and financial production. Even if other sectors are able to provide an income that may be higher than that of dairy cows (e.g. dairy goats), the beef sector is very large (with many producing countries), the cows produce a higher quantity of milk, and the larger and less agile animals allow the robots to work more easily.
The rest of the livestock robots, however, are struggling to develop strongly. While small cleaning robots still seem to be affordable, the price of feeding robots (e.g. automatic concentrate feeders) is approaching that of milking robots, but the return on investment of such a device may not be as justifiable. In addition, even if feeding robots are able to individualise concentrate rations, they are not yet able to individualise the whole diet of the animals – especially when forages are considered.
A focus on crop production
In crop production, the main orientation of robots seems to be towards labour-saving, with the logic of automating existing agricultural tasks or making them more efficient. Bear in mind that this model could be undermined if regulations require the presence of an operator to supervise the robots (more on this later). Like any emerging sector that is still searching for answers, the robotics sector has chosen fairly simple entries, the main one being the substitution of chemical weeding in the rows (Figure 4), because the regulatory constraints on the reduction of the use of phytosanitary products are growing and the need for manpower is a major issue for several sectors of agriculture.
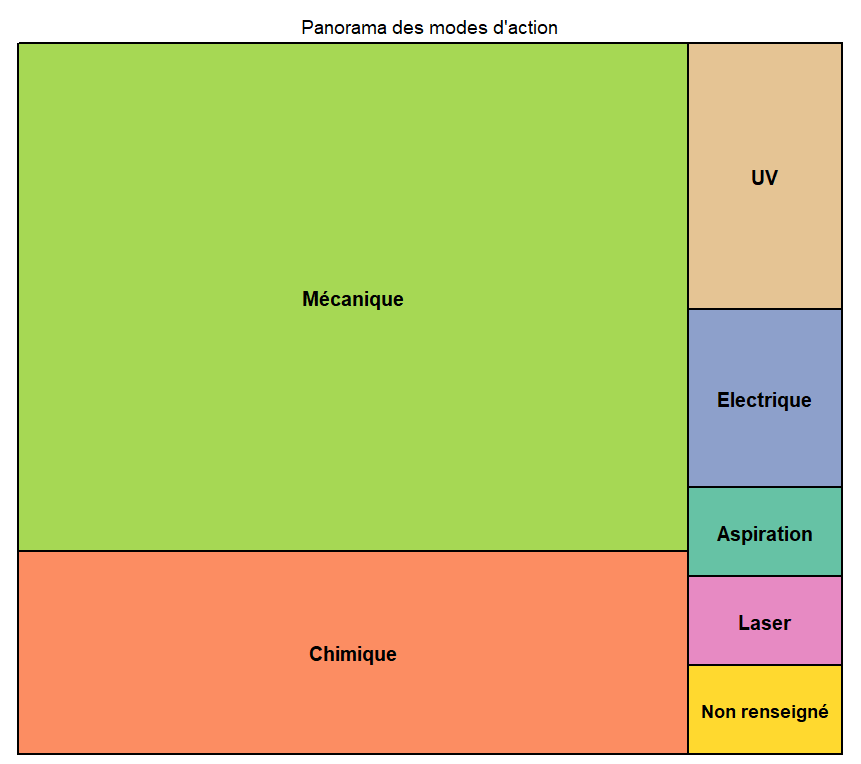
Figure 4. Overview of robot modes of action in crop protection. The size of the boxes represents the proportion of robots using this mode of action. Source: Directory of digital tools for farmers Translation by box size : Mécanique (Mechanical), Chimique (Chemical), UV (Ultraviolet), Electrique (Electrical), Aspiration (Aspiration), Laser (Laser), Non renseigné (Not Filled)
Just as the distinction between animal and crop production is necessary, it also makes sense to look at the crop sectors from different perspectives (Figure 5).
In horticulture crops, roboticists are mainly concerned with labour issues and the drudgery of repeating agricultural tasks (especially if we are talking about chemical substitution and/or the switch to organic farming, which will require even more regular visits to the plots). Some activities are not even feasible with conventional agricultural equipment, such as asparagus harvesting, which requires detecting the tips and following the growth to cut in the right place, and which therefore requires manual or robotic harvesting.
Robotic proposals in arboriculture are still relatively undeveloped because the working environment is complicated by the varied plant architecture, which is not always homogeneous within the same orchard, and with obstacles that can hinder the navigation or vision of the robots.
In viticulture, the development of robots is quite important. The roboticists are perhaps more inclined here to put forward marketing arguments – with even more “ecological” wines and with fewer phytosanitary products. The development in the sector is mainly driven by the large wineries that have the means to support or buy robotic tools. In viticulture and arboriculture, it is not so much the price of phytosanitary products (which is actually quite low in relation to the total costs of the farm) that is pushing farmers to take an interest in the subject, but rather the fact that professionals have understood that chemical products, especially for weeding, may soon be outlawed. The question arises for small vineyards (a few hectares or tens of hectares) which will find it difficult to replace their chemical products without financial support. Changing their weeding methods – whether or not they use a robot – will require them to buy a new machine (robot or tractor) that they are not sure they can pay off on small plots.
Robots are also starting to interest the seed industry, with seed multipliers wanting to achieve species purity that meets standards. Robots are also being developed in greenhouse contexts (vertical and horizontal greenhouses), where the environments are generally fairly structured and production is fairly standardised (the plants are rather adapted to robotic handling). Navigation between rows is relatively easier and the infrastructure in greenhouses is often an aid to the movement of robotic units (overhead crane, rods, arches…). The logic of automation in greenhouses is more or less advanced and generally meets the expectations of the population in terms of regulations (organic products).
In field crops, there are not too many robots in operation because the cultivation itineraries are still very mechanised (figure 5 shows that roboticists are nevertheless interested in this area, whether by developing autonomous tractors or tool-carrying robots). The environments are much more open, and the soils are not necessarily always as loose and/or fine as in horticultural crops. The use of robots for specific tasks in field crops raises questions with regard to the diversity of crops and management methods (sometimes even different between two consecutive years on the same farm). Proposals seem to be turning towards modular tool carriers to which it will be possible to attach the tools already present on the farm (with standard 3-point attachments like on tractors). Some manufacturers are also moving towards autonomous tractors, without cabs, with just intelligent guidance, to which everyone will once again attach their tools of interest. Some tasks may be complicated to automate anyway, for reasons of connection to the land and to the work – think of sowing or harvesting, which are still very much a matter of the farmer’s sensitivity and knowledge of his farm.
Across all sectors, robots are being developed for monitoring and inspection applications in agricultural plots (presence of insects, detection of leaf spots, weed detection, detection of the start of infestation outbreaks, yield estimates, etc.) with autonomous systems incorporating monitoring tools (visible cameras, multispectral cameras, etc.). These robots are sometimes dedicated to monitoring or take advantage of their visits to the plots to add this functionality.

Figure 5. Overview of robots by commodity chain. WARNING: the figure is very theoretical because some robots are highlighted as being able to work on certain commodities but this has not necessarily been demonstrated. Source: Directory of digital tools for farmers Traduction from left to right : Bovin (Bovine), Maraichage (Vegetable crops), Grandes Culturales (Arable crops), Viticulture (Viticulture), Ovin (Sheep), Caprin (Goat), Arboriculture (Arboriculture), Prairies (Meadows), Porcin (Porcine), Aviculture (Poultry farming), Aquaculture (Aquaculture)
A more technical entry into robotics
The main types of robotic machines
Entering the robotics sector through a technological prism (Figure 6). allows us to observe several paths of robot development:
- The proposals for autonomous tractors seem to be there to limit labour problems but do not propose a change in the agricultural model. The active tools are attached to the tractor, which is either manually controlled or works autonomously.
- The regulatory constraints mentioned above are pushing for a paradigm shift to produce differently rather than automate existing tasks (some may not see this as a paradigm shift, but that is another subject for debate). In this case, robots often fulfil a fairly specific function (weeding, spraying, mowing, etc.) and will mainly make it possible to reduce or stop the use of phytosanitary products.
- The robotics sector also offers tool carriers whose objective is to increase the multifunctionality of robots by giving them the capacity to be present in many agricultural activities (weeding, trimming, tilling). These tool carriers are close to the notion of an autonomous tractor but are really designed to adapt to different tools and are especially lighter than autonomous tractors.
- Some players in the ecosystem do not propose robotic tools as such but rather embedded tools that will allow tasks to be automated (on-board cameras at the front of a tractor to automate hoeing or spraying at the rear of the tractor).
- There will also be cobotics or human-robot cooperation tools in several formats. The human operator complements the automatic sensing capabilities of the autonomously navigating robot by performing additional verification and correction of the robot’s perceptions. The robot can also act as an assistant to lighten the load of arduous and possibly dangerous tasks (e.g. following robots) or to reproduce an operation in parallel to that of an operator present in the field (harvesting, spraying…). The operator can also be installed on the robot to perform cooperative handling tasks (harvesting lying on the robot).
- Still young approaches to cooperation between robots (or swarms of robots) are beginning to emerge, either simply between several ground robots (to carry out single tasks together or to combine for more complex tasks such as transporting heavy loads), between ground robots and aerial robots (mainly drones) or between several robot arms on the same mobile vector. We can then observe leader-follower approaches, with inter-robot communications coordinating movements according to the state of progress (a bit like in the case of a robot following a human except that the human is here a robot or a main tractor)

Figure 6. Overview of robot technology directions. Source: Directory of digital tools for farmers Translation from left to right : Robot monotache (monotask robot), Robot multi-tache (multi-task robot), Porte-outils (Tool Holder), Tracteur autonome (Autonomous tractor), Robots en essaim (Swarming robot), Cobot (Cobot), Bras robotisés (Robotics arms), Robot téléguidé (Remote controlled robot), Outil d’automatisation (Automatisation Tool)
Agricultural tasks are still complex for robots to perform
Robots are still struggling to work in non-standard environments. In France, the vast majority of robots sold are milking robots (Lachia, 2018) and these robots are fixed – it is the cows that move. Being fussy about the definition of agricultural robotics, one could actually question the terminology of ‘robots’ for these milking devices. Generally speaking, robots are indeed more at ease in fairly flat and gently sloping topography, with well-maintained plant material, and with relatively generous climatic conditions (good sunshine, little dust, no rain, etc.). This is also one of the reasons why many roboticists have focused on specialised crops, often in rows (where rows, inter-rows, and intra-rows are clearly distinguishable) and on certain farming tasks rather than others, namely tillage or weed control.
When these conditions are not met, the interventions of robotic machines are immediately less effective. It must be said that there are many difficulties. Robots already need to find their way around complex plant environments that are constantly changing during the season. Vision and image recognition technologies have long lagged behind because the answers were not satisfactory. With the revolution in computer vision and in particular neural networks (for interested readers, I refer you to previous blog posts) from 2012 onwards, hopes of being able to automate agricultural tasks with robots and bring projects back from the drawing board have reappeared. However, these hopes are only confronted with a painful reality: the problems of perception in agriculture, i.e. the robot’s ability to picture the world around it, are very complex, variable and difficult to master.
In perennial crops, leaves and branches can interfere with the robots’ detection capabilities by obscuring the objects to be observed (fruit, leaves, etc.). Disease or deficiency spots that are potentially observable in a well-controlled laboratory environment may be barely distinguishable on the images, either because of their size – sometimes millimetre-sized – or because they need to be particularly well identified to avoid discretionary constraints in the images. Keep in mind that when visual symptoms appear – even if they are detected by the images – it is sometimes already too late. Moreover, early detection of diseases, especially by hyperspectral imaging (using many different wavelengths) seems to have fallen into a pit of disillusionment insofar as many diseases generate the same stress effects on the plant (it is therefore difficult to distinguish between them) and, once again, when the symptoms are visible, it is sometimes the case that the phenomenon to be observed has already exploded and can no longer be stopped. Some players have refocused on very high spatial resolution imaging rather than spectral imaging, considering that human vision, with much higher resolution, is still the best way to make observations.
Shading, low sunlight and overexposure generate countless artefacts in the images that the robot has not learned to consider. Dust, rain or fog will reduce the quality of the images. Roughness, stoniness or topography of the terrain will affect the stability of the robot and create vibrations that will result in biased image quality. The diversity of fruit shapes and colours within the same plant environment (biscornus, flat, round or more or less ripe fruit) will make it even more difficult to discriminate fruit ready for harvesting. Distinguishing weeds within plots (e.g. datura) may be easier at some stages of development than at others.
These perception problems require a huge number of well-labelled image banks so that the robot can learn to recognise what it is being asked to recognise. Between the multiple environmental configurations, crop maintenance or cultivation practices, you can imagine that a few images are not enough to represent the diversity of points of view that the robot may have in the field. It is important to understand the difficulty of generalising vision and recognition algorithms in agriculture. In imaging, scientific work is published as soon as the algorithms seem to work on a few hundred images. However, the work suffers from a delicate transition to scale from the moment when larger agricultural contexts must be considered (small agricultural region, different terroirs and practices, etc.). Labelling images is extremely time-consuming (and therefore costly for an industrial company) even when using tools or support software that mix supervised and unsupervised algorithms. Work is underway to move away from these databases and learning to so-called “unsupervised” methods but, given the current performance of vision under supervised conditions, it is reasonable to ask how the robot will be able to cope on its own. Other research focuses on building simulated environments or ‘models of the world’ (agricultural plots and artificial unstructured environments…) in which hardware simulations could be run in a loop. You will certainly also hear about digital twins. However, the ability of these devices to capture the variability that can be observed in the field remains to be questioned.
These notions of vision and recognition are at the heart of the challenges of robotics as it is decided that robots will be able to make precise gestures, close to those of humans and conventional machines. Plant handling, especially for picking and harvesting, requires robots to have extremely precise gestures so as not to damage the fruit/seed/vegetables to be harvested (bruising, points of contact) and a solid gripping capacity to be able to perform as many tasks that might seem simple to a human, such as turning a fruit, cutting off a stalk or filling a pallox with fruit (the conveyors on robots are still sometimes too rough for the fruit). The robot’s vision must be qualitative in order to distinguish between two fruits of different appearance so as to pick only one of the two fruits and avoid shocking the second if it is not ripe. In general, shocks in the plant environment can lead to a lot of fruit falling off and to yield losses (e.g. in the case of suction harvesters that are too violent or robots that touch the plant too regularly). Note that the issues are not the same between fresh and processed fruit. The robot arms must be extremely mobile to work in several different axes (inclined, parallel to the plant, etc.). The multiplication of robotic arms, each performing one task, remains a possibility but will increase the cost of the robotic units proportionally.
There is also the complexity of guiding the robot within these complex environments (Figure 7). If camera vision remains an aid to robotic navigation, geo-positioning technologies remain the main choice of the sector’s players, with cameras and/or Lidar being used more for obstacle detection or to make the robot safe in the event of human and/or animal presence. Geo-positioning signals can be greatly affected by the plant infrastructure in place, with for example reflected signals (I refer you to another blog article to talk about geo-positioning) and/or blocked satellite coverage. And the result is all the more worrying as the geolocation precision must be fine. In unstructured 3D environments, some of the limitations of GNSS or RTK positioning can be reduced by combining geo-positioning technologies with vision tools (RGB camera, 3D camera…).

Figure 7. Overview of robots by guidance mode. Source: Directory of digital tools for farmers Translation from top to bottom : Télécommande (Remote), GPS Indoor, Aléatoire avec détection d’obstacles (Random with obstacle detection), RTK et Caméra (RTK and camera), Caméra seule (only camera), RTK et Lidar (RTK and Lidar), Laser / Lidar / Radar / Ultrason (Laser / Lidar / Radar / Ultrasound), Fixe (Fixed), RTK seul (RTK alone), Non renseigné (Not filled), Aimants / Fils / Rails / Puces RFID / Transpondeurs (Magnets / Wires / Rails / RFID chips / Transponders)
The integration of robots in the field will require the ability to accurately assess robot performance, certainly by breaking down the tasks to be performed. What is good recognition? What is the right action? It will also be necessary to ensure the reproducibility of robotic agricultural tasks in a variety of environmental conditions – slope, dust, etc. – and we have explained in this dossier that this is a relatively difficult task. It will be difficult for the robot to achieve truly human-like levels of performance, especially for complex tasks, but we will have to ask ourselves whether there is really a problem with this. However, tolerance levels will still need to be defined to assess when these lower performances will remain economically and/or ecologically reliable. Let us add that the evaluation of a robot’s performance will also be difficult to transpose between different countries, as the means of work (driving methods, work organisation, etc.) may differ.
Some speeches are perhaps still too optimistic about the evolution of these technological issues. I am not saying that these barriers will never be lifted, but that a little pragmatism and realism are in order. The asymptote of maturity for these robots has not yet been found. There are many technological obstacles:
- The development of elementary behaviours will allow robotic machines to be even more autonomous. It is important to understand that robots will have to be able to change their sensory and motor behaviour on their own, i.e. depending on the context and the task to be carried out, the robot’s behaviour will have to be able to adapt. Between tracking a trajectory by GPS, following a footprint on the ground, tracking a person by laser or Lidar or following an already installed structure, the robot will have to be able to change its operating mode to adapt to the constraints of the moment and to its mission.
- The modularity of the robots and their ability to perform several tasks will make it possible to increase their rate of use in the field and to be more widely shared. This modularity will also facilitate coordination between several robots, but poses many challenges in terms of how to synchronise and associate robots to carry out common tasks
Robot size and work rates
The approach to machines in agriculture has always been to go for the gigantic, with ever larger plots and ever larger tools to optimise workloads and working times. Even if robotics could still take this logic to the extreme (we will discuss this again), most roboticists are still tending to reconsider the size of robotic systems and to propose (much) smaller units than their conventional cousins.
Smaller robots are interesting in several ways. They can already reduce soil compaction because they are lighter and one could imagine that this reduction in size could avoid losing yield by simply having too much soil compaction (could this money saving offset the cost of an operator to supervise the robots?). Working with small robots facilitates the development of electric mechanisms to propel the robots and thus goes hand in hand with the need to decarbonise agricultural activities. Smaller robots will allow quick rotations between work units, with punctual and fine interventions, and robot recharging will be quicker, which will allow to have always active units during the day. In the event of a seeding problem, reseeding will be possible in the sense that conventional equipment, which is too heavy and inflexible, would cause too much damage to the growing crop. The miniaturisation brought about by robotisation is a real value but it has its limits. The capacity of robots to work is constrained by their power-weight envelope – it must be understood here that by reducing the size of robots, we also reduce their capacity to carry out tasks that require power – such as tilling the soil.
Several scientific studies tend to show that autonomous machines would enable a farmer to achieve minimum production costs on a smaller scale than would conventional equipment. The ability to achieve low production costs at relatively small farm sizes, and with modest equipment investment, means that the pressure on agricultural businesses to continually seek economies of scale could finally be put aside (Lowenberg-DeBoer et al., 2021). The costs of investing in robotic systems could even be greatly reduced if small agricultural robots are used very intensively. Going a step further, one could therefore imagine that small robots could almost eliminate the competitive advantage enjoyed by the large rectangular fields of the dominant agricultural model.
The field rates of today’s robots are lower than those of conventional operator-controlled machines. But is it really that bad? It all depends on where you stand. The conventional tractor was mainly positioned with the objective of maximising hourly profitability at a time when performance objectives were certainly not those of today. It is now necessary to find compromises between the agility of robots, the diversity of cultivation conditions, and the maintenance of soil conditions.
From a more operational point of view, some agricultural tasks do not fundamentally need to be done quickly. Weed control, for example, can be carried out over several days, provided that it does not allow time for weeds to set seed and that, more generally, the development stages of crops and weeds are properly considered. On perennial crops – such as vines – it will also be necessary to consider that not all weed control is the same. For example, in-row weeding is much slower than inter-row weeding in grapevines, and it will be necessary to weed more times in the rows than between rows during the crop cycle. In periods of high flow – such as harvesting – the issue of throughput could be of much greater concern.
Various business models
Robots are expensive – tens or even hundreds of thousands of euros – and robotic systems alone may need to be complemented by other infrastructure, increasing their price even more. Take, for example, the cost of a robotic arm for harvesting, to which must be added a self-guiding platform, the development of detection software, the gripper or the mobile architecture. And I’m not even talking about the cost of insuring autonomous equipment, which, if it turns out to be high, could clearly play a role in the balance (insurers are beginning to take a renewed interest in the subject of robotics). The amortisation of these robots has focused on the high labour requirements and it is not surprising that a large proportion of robots in crop production – often single-handed – are dedicated to activities such as weed control for high value crops. Some field tests have shown that regular mechanical weeding in horticultural crops could lead to yield increases thanks to increasingly high weeding efficiency (so it’s worth looking into…). On the other hand, in order to achieve economies of scale and reduce the price of robots (and to have spare parts…), it will be necessary to cover (very) large areas and to be able to work on other production systems, particularly field crops.
Note also that with the current supply problems and shortages of raw materials, manufacturers sometimes have to place large orders and keep stocks to avoid heavy variable costs. Some branches of robotics are nevertheless beginning to move towards low-cost aspects with the desire to use low-cost mechanical structures and sensors (e.g. smartphone connected to a modular structure to guide the robot via a smartphone application, robotic arms or a fleet of robots with different degrees of mobility, etc.)
Considering the number of robots sold in crop production (a few hundred), it is difficult to believe that robotics companies are profitable. These structures seem to live on their cash flow and are subsidised by a whole host of funds dedicated to innovation (European, French), private investments, and potentially bank loans. The French recovery plan could also be put to work with a major robotics challenge which, if accepted, could direct some twenty million euros in all directions towards the agricultural sector, from innovation to challenges and demonstrators. The development of robots and their potential adoption takes time anyway and investments in the sector are made over the long term. It can be observed that some robotics projects stop or fade away as soon as they have no more funding. The players in the robotics sector are quite varied. We can find :
- Technology providers, already established in other industries (with their own navigation, control, and sensor systems), who have identified agriculture as an attractive area.
- Start-ups, mainly technology-oriented, that enter the market with specialised, often small robots or technologies to be adapted to the robots.
- Agricultural machinery manufacturers, with a long tradition of mechanical engineering, more or less advanced in robotic systems. These players generally either upgrade their automated machines to autonomous systems (with retrofit systems, for example), or develop new robotic systems by capitalising on their knowledge of traditional machines. Note that some of these players will prefer to buy robotics start-ups to internalise these skills (e.g. John Deere which bought Blue River Technology and Bear Flag Robotics). Some manufacturers of robotic agricultural machinery prefer to focus on a functional robotic system without necessarily going too far on the embedded intelligence behind it (adapting the tool to the constraints of the field using machine operating data, using vision data, etc.), this section being rather outsourced to a partner. It is understandable that with the diversity of skills that need to be mastered, even if only to make a robot work (navigation, energy management, tool coupling, etc.), manufacturers do not want to add skills in vision or data analysis.
- Equipment manufacturers who do not build agricultural machinery in their own right but who develop agri-equipment to be installed on manufacturers’ agricultural machinery. One might wonder whether these equipment manufacturers are not interested in robots to reduce their dependence on agricultural machinery manufacturers by having their own power source. These manufacturers may indeed need to have their own on-board computer and associated intelligence and may want to have their own mobile support
In the plant context, as the price of robots is currently quite prohibitive (at this price, farmers can buy several conventional agricultural machines), manufacturers seem to be turning mainly to the rental of robots (even if some continue to sell robotic systems individually) with or without a subscription logic. Manufacturers can also rent single robots or fleets of robots. Some manufacturers are also starting to move towards a service economy (e.g. the sale of a hectare of weeding or mowing), a service that could then make more sense in the context of a work service or for the shared management of robots. The proposed rental and service models are not so surprising given the maturity of the robots proposed. Most of the robots are still in the testing or development stage (I have not taken any figures from the digital tools platform because the information is too uncertain on this subject), and are not yet reliable enough for autonomous use by farmers. The prototypes are not yet perfect, regularly break down and are not easily repairable. These models under development also allow manufacturers to consolidate their feedback from the field. The manufacturers are also waiting for tests to be carried out on a larger scale, with the support of consolidated structures such as cooperatives. The question sometimes arises of the availability of robotic equipment so that these structures can test robotic tools that are sometimes barely marketed.
The use of autonomous robots on farms calls for reflection on interesting questions of collective organisation and logistics. Insofar as current robots are mainly task-specific and given the current price of robots, the mutualisation of robotic units appears to be a relevant proposal. Are the robots suitable for use in a cooperative union of agricultural equipment (CUAE), for example? There are many answers to be given in terms of work sharing, transport of the robots (should a trailer be bought in the CUAE?), recharging (on a mobile terminal or in the CUAE shed), responsibility (a CUAE member or employee), economic relevance (is the purchase of the robot worth it?) or strategy (should autonomous tractors be considered in the context of the renewal of the machine fleet?) One of the current limitations is nevertheless the lack of reference from CUAEs on these robotic devices.
The first robots purchased by agricultural actors are often quite heavily subsidised because existing aid is directly targeted at the purchase of innovative systems. One might question the fact that little aid is still directed towards service provision or subscription. By favouring aid for purchase, the subsidy system in a way encourages indebtedness and does not take into account potential shared purchases and usage rates, which are ultimately quite low if the robots are not shared (especially as they are also mainly single-client).
As the panoramas have shown, the manufacturers’ proposals are quite different, ranging from highly specialised single-task robots (which are still the majority of robots), to multi-task robots, tool carriers, cobot systems or even cooperative robot systems. And the associated business models of manufacturers are varied. Some will position themselves on one and only one robot, while others will rather have a logic of a range of robots with robotic systems tackling different tasks within the same sector or systems tackling the same task but between different sectors. We are also seeing the emergence of a logic that could be called full-liner with the idea of a robot or a fleet of robots that can manage a crop itinerary from start to finish (from sowing to harvesting) without any human intervention.
It is surprising that many manufacturers of robotic systems do not use standardised architectures and redevelop their robots from scratch. Couldn’t we imagine a more industrial logic (which would lower costs) with modular bricks (mobile vector with wheels, batteries, etc.)? For example, companies that develop digital services based on drones mainly use drones on the market and do not redevelop their own drone each time.
The segments in which robots operate are not always clear (even to roboticists) and there is a clear lack of mapping of robotic maturity and segments. For which crop, variety, phenological stage, or farming context is each robot mature? Where is the solution now and how far can it go? Some manufacturers might see this as a risk of competition, probably wrongly so, but this mapping would allow the agricultural sector to see much more clearly.
Generally speaking, since agricultural investments are planned with long payback periods, it is necessary to demonstrate very pragmatically that robotic solutions do indeed offer a satisfactory cost-benefit ratio (which will also make it possible to no longer depend on subsidies and to offer more independence to agricultural actors). The majority of studies in the scientific literature have been able to find scenarios in which automation and robotic technologies are cost-effective. It should be added that the diversity of results concerning margins, yields and profitability does not allow for obvious general conclusions. Nevertheless, it is important to note that most of these studies only considered costs and revenues that were directly changed by the introduction of automation or robotics, assuming that everything else was constant. Oversimplification misses the implementation of the robot in a much broader agricultural system and its implications on as many parameters as changes in cropping systems, the value of data that robots might collect while performing other tasks (even if this is difficult to measure), regional and national impacts on markets, trade, or labour demand (Lowenberg-Boer et al., 2021). Perhaps we should also start thinking about economic models that are not organised around the farmer? Could we imagine robots working on grassed strips in the framework of the directive on the non-exposure of residents or on revegetation systems, with an economic model where the robot does not depend solely on the farmer but, for example, on local territorial funding to protect residents, a water catchment area or a sensitive tourist site? Cumulatively, these surfaces are far from negligible and could make it possible to achieve scale effects in a way that is quite different from what is proposed today.
Important regulatory issues
Despite their detractors, the use of robots in the agricultural context is still quite restrictive under current regulations. The problem is therefore not so much how to develop a driverless tractor (this is not a technical problem after all) as how to regulate it.
There is no specific regulatory regime for agricultural robots or for robots in general. Indeed, one might wonder whether a single regulatory regime would make sense, given that robotic systems are so different from one another, whether in terms of their functions, their level of autonomy or their level of human-machine interaction.
At European level, the main regulation that applies to agricultural machinery is the Machinery Directive 2006/42/EC (which dates from 2006). This regulation governs the main operating and safety principles with which manufacturers must comply before placing machinery on the market. In order to comply with these requirements, manufacturers apply European and international standards (EN and ISO), which are harmonised with the regulations and which serve as a guarantee of conformity for their machines. This directive is due to be transformed into a machine “regulation” in the course of 2023 to incorporate the main developments in robotic systems (recognition systems, robotics, autonomy and autonomous movement, protection against intrusion, cyber security, etc.). Once the regulation is published, all the standards will have to be revised to take account of this new information.
From the outside, this regulatory work looks like it’s going to be a bit slow. However, on closer inspection, it becomes clear that there is no consensus on certain aspects, particularly on the issue of robot supervision by an external operator, and on the fact that the regulatory context does not stop at this single Machinery Directive. The question of a compulsory supervision post is crucial for the sector. Imposing it would already mean going back on a number of things for robots that are already widely used by the public (for example, mowing robots). The need for an external operator would have a very significant impact on the business models of the robotics sector since this operator would not necessarily be able to perform other agricultural tasks alongside the robot. Stakeholders wonder whether supervision could not be carried out remotely. In any case, questions will arise about the responsibility of the operator, who is not always present with the robot but is legally responsible for the safety of operations. The operator must be able to put the machine in a safe position at any time.
Everyone fears accidents (a child in a field, a human crouching down…) and these fears are legitimate and real. Robotics manufacturers have quickly agreed on the need to work together on these safety issues to prevent one of them from affecting the image of the industry as a whole. The players are making collaborative contributions in terms of safety at OECD and ISO level (choice of sensors for detection, certifiable anti-collision approaches, analysis of typical failure modes, safety rules, geo-positioning accuracy, maintaining the physical integrity and controllability of robots, etc.). An alternative could be to install fences to prevent any involuntary interaction between the robot and man, but it is difficult to imagine this being realistic from an operational point of view (not to mention the impact on local fauna and the additional investment required to set up these fences simply to be able to use a robotic system). As safety issues are paramount, one could imagine the use of a social consensus on the residual risks associated with the use of automated machines.
Another issue is the working speed of robots, which is directly related to the throughput of robotic systems (with the potential need to be registered if these systems are to be used on the road and sometimes with maximum travel speed criteria). It is therefore reasonable to ask again how agricultural business models with robots would respond to changes in site speed. A speed restriction could make autonomous machines uncompetitive with conventional agricultural machines on mechanised farms.
Several other regulations are also adding to the game. At the European level, the Mother Regulation (EU Regulation 167) deals with the approval procedures for agricultural tractors. At present, this regulation does not allow for “type approval”, i.e. the provision of proof of conformity of the tractor type with the regulations in force by an accredited body (approval here is more of a regulatory nature and has nothing to do with the approval of an autonomous tractor on its farm). There are also road traffic regulations for machines that use our roads. There are already specific criteria for self-propelled agricultural machines (MAGA regulation) which only travel on roads under certain conditions (e.g. combine harvesters). This regulation includes several criteria such as braking distance and the width of the lane that can be used by the self-propelled machine. For general road traffic, road regulations and traffic rules apply (in the same way as for autonomous vehicles) and this is where the problem lies. Agricultural robotic systems may indeed have to cross roads to link two nearby plots. Some alternatives have been proposed to adapt the Machinery Directive (for example by moving robots on a trailer – transport on trailers is allowed under the current directive) to avoid tackling road regulations, at the risk of impacting the business model around the robot. Finally, let’s add that these regulations are combined. A combine harvester with an autonomous mode, for example, will be subject to the MAGA regulation and the Machinery Directive.
One thing is certain: the regulations must be followed closely as they may completely transform the interest or not of integrating robotic units in the fields.
Impacts of robotic systems in agriculture
A quick look at the potential fractures in agricultural robotics
There are many risks of fractures likely to appear following the deployment of digital technology and robotics. I invite you to reread a previous blog file where I gave a lot of space to authors from the human and social sciences on this issue. Without going back over the subject in detail, you will find here some non-exhaustive fractures detailed in the previous file, but focused here on robotics:
- “Digital divide”: The development of robotic tools could risk increasing inequalities in access to tools in the territories. We could indeed fear the development of white zones where dealers would not want to deploy in order to avoid having to manage robotic breakdowns on farms that are too isolated. The roboticists could be led to size the geography and density of their network on the territory, and to constrain their distribution networks by transport logics to optimise their movements and reduce their costs, thus leaving aside a part of the farms and their access to robotic units. One could also add the concept of white zones in terms of network coverage, which could limit the possibilities of self-guidance in certain poorly covered areas.
- “Precision divide”: Robotic tools have so far mainly focused on value-added crops, notably vegetables and some perennial crops. We are referring here to the fact that on the one hand, there would be industrial crops in a simplified ecosystem, very largely monitored and accompanied by robotic tools, receiving sufficiently good and precise advice, and on the other hand, more diversified crops, for which the tools and advice would be of lesser quality and poorly adapted to their operations, and which would derive little benefit from the ongoing digitalisation.
- “Social divide: Robotic units will require new electronic and digital skills in the field – skills that may not be available to farmers if they are not properly trained, and which may favour employees from outside the farming world. We could indeed see the development of the profession of robot supervisor because the parameterisation of robots is very important and can have a huge influence on the robot’s ability to function properly. This social divide could be an opportunity to question the idea of a tax on agricultural robotics
- “North-South divide”: Conventional agricultural machinery has mainly contributed to the enlargement and geometrisation of agricultural plots. Robotic tools adapted to small agricultural areas could be a way for agriculture in developing countries to avoid the pitfalls of motorised mechanisation. However, it is clear that current robots have mainly been developed in westernised contexts and that their direct transfer to other contexts will certainly not be appropriate.
- “Technological lock-in”: in line with technological digitalisation, it is not impossible that the technical complexity of robotic machines, the parameterisation of the software, or the dependence on updates will tie farmers’ hands to the roboticists. There is also the risk that farmers will only have a licence to operate or use the machine, but will not be able to repair their autonomous machines (right to repair one’s work tool).
- “Change of scale”: If we imagine that robots will be able to automate a whole range of agricultural activities, we could expect that there would be no limit to the size of farms in the sense that the number of robots would simply be proportional to the area to be worked. Taking this to the extreme, could we imagine a farm in France with one person controlling the entire production?
- “Financial security of farms”: The current cost of robots raises questions about access to this type of machine and the possible debt that these robotic systems place on farms (repairs, maintenance, upgrades, etc.)
- “Safety and cyber security: autonomous machines can be responsible for accidents to humans (either directly if the machine is not able to detect a presence, or indirectly if an autonomous machine crosses a road for example). Attacks on robotic units are possible, whether on the hardware, firmware or communication systems of the robots, with the possibility of taking control of the autonomous machines and affecting the safety of humans or crops around the robots.
- “Standardisation of production”: Due to the standardisation of food products needed to facilitate the early applications of robots, consumers may come to expect even more from all food to be perfect, which could lead to an increase in food waste as fewer items are deemed fit for sale.
- “Animal welfare: Although some authors point to a co-evolution of animals and humans with livestock robots (especially milking robots), the evolution of the relationship between humans and animals is open to interpretation. The fact that some cows are milked four times a day could be seen as a more refined consideration of the animals’ needs or as a result of increased agricultural productivity (hyperproduction, selected animals, etc.). Perversely, the reduced presence of human witnesses around robot activities could encourage greater tolerance of animal damage and thus exacerbate threats to animal welfare.
Towards labour savings and reduced drudgery?
The reduction of drudgery and the response to labour shortages are certainly the two main entry points for robotics players. Robotic units have a direct impact on working conditions on farms. For example, robotic milking reduces the workload and offers flexibility and greater freedom in working hours. The actual working time is not necessarily lower (and is sometimes increased) and, although some farmers will have taken a step backwards on milking robots, the main users would have found a better quality of life. There is a real expectation among young farmers to be able to free up time and mental workload, even at the cost of a reduced margin. However, this image is perhaps more likely to be conveyed by neo-rural farmers who have experienced life in a company with a more rational organisation and acceptable workloads, and who do not necessarily want to call all that into question when they arrive in the fields. Even if the argument of time saving is sometimes put forward by roboticists in the sense that the autonomy of robots would free up time for time-consuming tasks, it will be necessary to ensure that the methods of measuring working time also evolve with the arrival of robots. The mental load and management of robot notifications and alerts, unit repair times or the time spent changing tools attached to robots are parameters to be considered in an overall analysis of working time.
In crop production, workers’ working conditions are also likely to improve if we consider that robots can reduce loads, reduce painful postures and limit musculoskeletal disorders (the example of robots in the form of platforms with operators lying down is a good example), limiting workers’ exposure to certain dangerous products (e.g. plant protection products), reducing exposure to vibrations and noise, limiting access to danger zones (e.g. in slaughterhouses) or limiting agricultural work under difficult environmental conditions (e.g. work in greenhouses in the middle of summer). In any case, there is no great need to break one’s back, and if the robotic machine can provide a solution, it would be a pity not to take an interest in it – whatever the machine proposed (exoskeleton, co-botics, etc.).
The problem of the lack of labour (seasonal workers, tractor operators, etc.) is always dangerous to tackle because it is indeed a reality on the ground, but because it is also exacerbated by current agricultural models and one could get the impression that farmers are digging the grave they are already in. In high-density population areas, and sometimes even with high unemployment rates, farmers are struggling to recruit labour – even for unskilled jobs – either because people no longer want to come and work there (and wage increases sometimes make little difference) or because bursts of economic recovery will have enabled people to be employed elsewhere. Some agricultural activities are very time-consuming and require labour over very concentrated periods of time (the harvest of certain crops lasts only a few weeks). The switch to organic farming, even if it is highly desirable from a health point of view, does not help matters. Phytosanitary treatments can be spread out over time, whereas mechanical weeding requires much more regular weeding, further increasing the need for manpower. However, one might think that seasonal and temporary workers would be more likely to return knowing that the heavy work will be done by robots.
Let’s try to take a step back
Where are we going ?
The majority of robots that have been developed are mainly doing the same thing as humans already do (Figures 8 and 9). The robotics industry wanted to put forward proofs of concept to show that robots could be just as efficient as humans in carrying out the same tasks as they do, and thus move towards automation to replace simple and repetitive human activities. The trend seems to be to add more and more on-board intelligence to robotic systems to be able to represent the plant world like humans, to be able to move around in it and to perform fine gestures. The problem was again taken through the prism of technology, starting with current systems and trying to fit robots into them. However, the robotics industry is increasingly talking about the desire to “land” robots on the farm, which is a sign that the players were looking at agricultural robotics perhaps a little too high and with a viewpoint that was a little distant from agricultural issues.
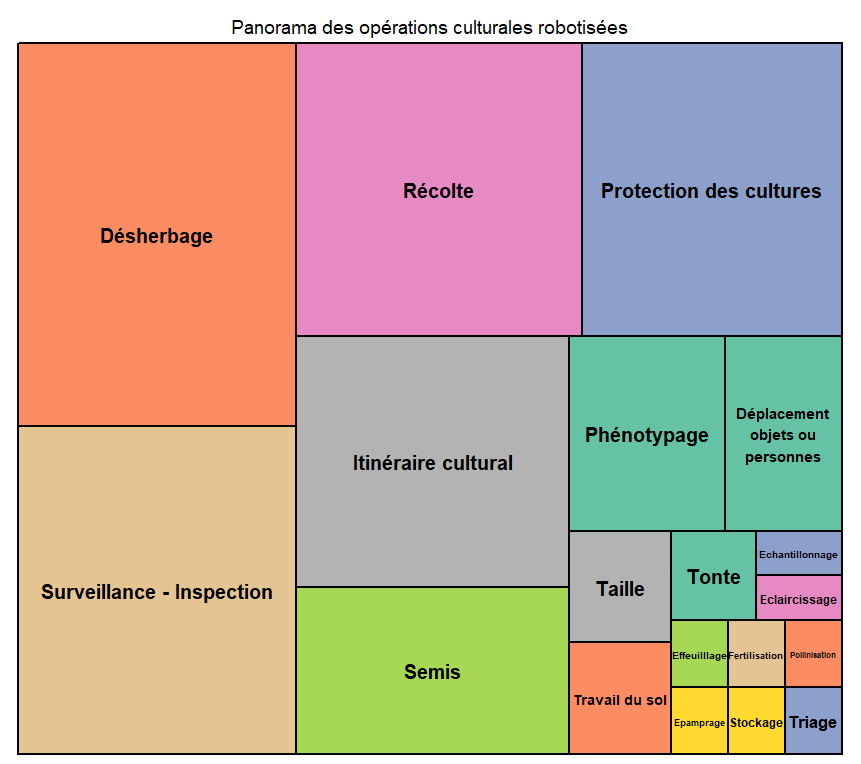
Figure 8. Overview of agricultural operations performed by robots in crop production. The size of the boxes represents the proportion of robots interested in this operation. The operation “crop routing” was mainly attributed to autonomous tractors for which the tasks to be performed were not clear. Source: Directory of digital tools for farmers Translation by box size : Désherbage (Weeding), Surveillance-Inspection (Scouting), Récolte (Harvest), Itinéraire cultural (crop itinerary), Semis (Seeding), Prtection des cultures (Crop Protection), Phénotypage (Phenotyping), Déplacement objets ou personnes (movement of objects or people), Taille (Pruning), Tonte (Mowing), Travail du sol (Soil Work), Echantillonnage (Sampling), Eclaircissage (Thinning), Effeuillage (Leaf removal), Fertilisation (Fertilisation), Pollinisation (Pollination), Epamprage (Pruning), Stockage (Storage), Triage (Sorting)
A first question to ask is perhaps whether agricultural stakeholders will buy a robot that does everything or a robot that does too much in detail. Full automation of a production process leads to a sub-optimal solution in terms of production cost. And we realise that for a robot, completing 80% of an agricultural task is easy enough, but completing the whole thing with the remaining 20% is devilishly more complicated (I invite you to re-read the beginning of the blog entry). So why do we put so much effort into research and testing to get the robot to achieve the 20% needed to fully automate an agricultural activity? Why are we asking the robot to think so much when the human brain is particularly good at it? Human-machine interaction offers interesting alternatives and would simplify the design of robotic systems even more.
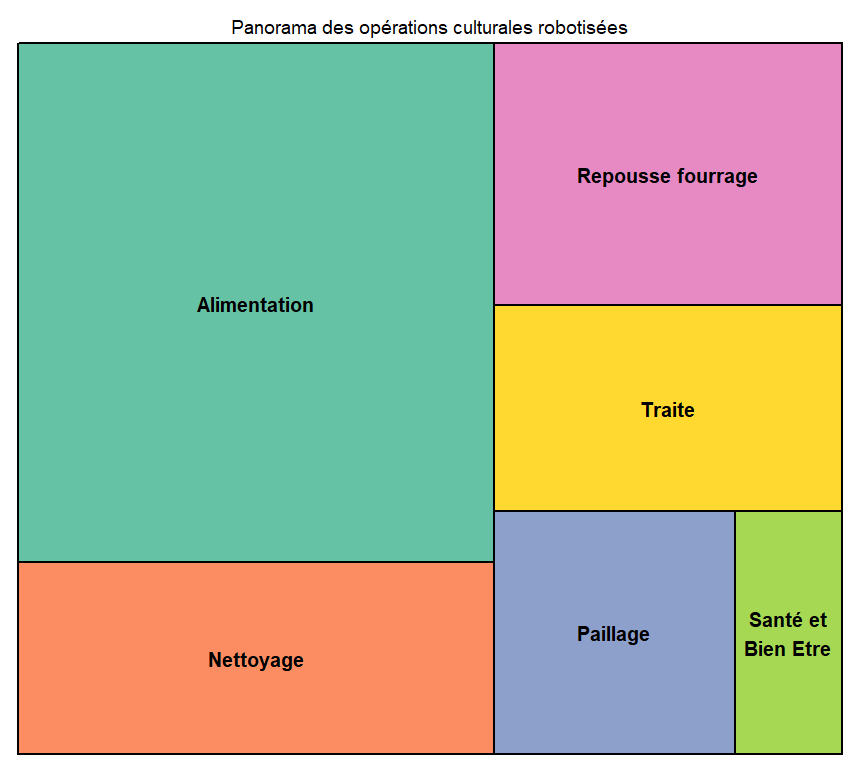
Figure 9. Overview of agricultural operations performed by robots in animal production. The size of the boxes represents the proportion of robots interested in this operation. Source: Directory of digital tools for farmers Translation by box size : Alimentation (Feeding), Nettoyage (Cleaning), Repousse Fourrage (Regrowth Fourrage), Traite (Milking), Paillage (Mulching), Santé et Bien Etre (Health and Wellness=
The robot could be designed mainly to limit the drudgery of work and to perform tiring agricultural activities. Melon picking, for example, is a particularly strenuous task for humans, requiring them to bend or stoop to pick up melons from the ground. Humans think fast and have a bad back, so how can we imagine a collaborative activity? The human could be lying down or reclining on an autonomous system for harvesting. One could also imagine that the human is only there to identify or tag the ripe melons which will then be harvested by a robotic unit, which would avoid having to install complex vision and recognition algorithms on the robots. The robotics sector could even propose exoskeletons without electronics, with harness and spring systems to accompany gestures, as is used in other industrial sectors. A great deal of attention could also be paid to follower robots, whether to carry heavy loads and leave the operator’s hands free, or so that the robot can do exactly the same thing as an operator in parallel (on the leader-follower principle). These devices would make it possible to double the speed of work and to comply with the regulations since an operator would be de facto present, but also and above all to help carry out work that the farmer cannot carry out alone (for example beet work). However, a distinction must be made between the automation of agricultural functions (harvesting, sowing, etc.) and the automation of safety functions (anti-collision detection, rollover protection, detection of leaving the work zone, etc.) and it is mainly on these second functions that manufacturers will have to set the cursor to know how to mobilise an operator who is doing something else at the same time. The robot system may or may not be able to perform its own monitoring and safety functions. If the robot relies on the human, the robot can be considered at best a highly automated machine but not an autonomous system. If the robot is not autonomous, then it will be difficult to imagine a strategy based on a nearby worker performing another task.
It is questionable whether current robots will be able to respond to the search for economies of scale insofar as they have been developed with electric motorisation logic (with electric storage) which is not compatible with high-powered operation over long periods. And even if this were the case, would it really be a problem? A system that does not respond to economies of scale must respond to different logics, and this could be the added value of robotic units, with modular autonomous machines, capable of performing different tasks, and on different crops. Systems that are more concerned with an economy of scale can be diversified systems that are compatible with satisfactory production on a plot scale, while being very efficient in terms of the environmental dimension. It is also possible to imagine robotics for the things we do not know how to do or cannot do, and thus to rethink the very way of working or even reimagining what a farming system is.
Thinking of robotics only in terms of labour savings is far too simplistic. At present, the health status of fruit crops (perennial or not) is monitored using meteorological data and an intervention schedule. Could robots be used to postpone or even avoid some of the intervention times? We discussed this above, but harvesting is a particularly difficult task for robots. Some do it, especially in greenhouses, but the work rate is particularly slow. Some of the slightly teasing interviewees told me that the current robots were capable of picking up fruit while damaging it and moving slowly… Rather than seeing robots only for harvesting, could we not imagine robots intervening to pick up damaged fruit? This activity entrusted to robotic systems would make it possible to limit contamination (and thus delay the first treatments and limit the doses applied) but also reduce the need for sorting at the end of the season. It is necessary to find situations where the action to be carried out is very important but not too complex for the robot to perform. In the same vein, robotic systems could be used to apply ultra-localized herbicide treatments to manage perennials (dock, thistles, etc.) before the farmer releases auxiliaries. Still on the subject of weed control, robots could be used to remove the few resistant weeds after a localised herbicide treatment to limit the problems of resistant populations. Robots could move into particular crops to vacuum up aphids or certain pests (no one would send an operator with a hoover into the fields). One could even imagine using robots to address public health issues by removing toxic or allergenic plants from pathways or byways that no one is responsible for. The challenge here will be to see how to make robots profitable where the return on investment is not necessarily immediate.
Robotics and agro-ecology
Could robots really accompany the agro-ecological transition that everyone is talking about? This is what the great robotics challenge proposed by the French association Robagri as part of the acceleration strategy “Sustainable agricultural systems and agricultural equipment contributing to the ecological transition” (SADEA) and the PIA4, which is part of France 2030, will seek to address. We could start by pointing out that it is not easy to say whether robots are suitable for itineraries that have not yet been invented… Robotics will not provide a solution or an answer to the impasses in which some agricultural systems find themselves. There are already many obstacles to overcome before the robotisation part on the understanding of crops and their interaction with their environment. Farmers lack agronomic knowledge and the risks involved in switching from a conventional standard itinerary to more innovative agronomic itineraries (limiting tillage, introducing companion plants, etc.) are not sufficiently supported. The current systems have difficulty being economically efficient and environmentally interesting. Some actors tend to say that current robots can be interesting until we have rethought our cropping itineraries (in terms of tillage strategy, practices, and soil), and some see them more as transitional toys. It must be admitted, however, that some changes in practices are also limited by current machines (e.g. sowing under cover). If robots are used to continue the same farming as today, we will be heading straight for the wall anyway. Perhaps robots should be thought of as tools and not as machines. The tractor by itself is effectively useless, it is just a source of power.
If we consider that robots have their raison d’être in the agricultural ecosystem, is it then up to the robot to adapt to the plot and the agricultural itineraries, or is it the plot that should facilitate the action of the robots? In reality, the cursor may lie somewhere between the two: the tool must co-evolve with the technical itinerary. And this co-evolution is necessary to avoid the risk of being stuck on certain types of itinerary and of creating a barrier to change. In any case, it is difficult to reason with the current agricultural system, which is not fixed. We can indeed expect that the development of robotics will lead to a form of standardisation of plant material and practices – without necessarily seeing this as an absolute evil. For example, robotic mechanical weeding may lead to a review of the spacing and alignment of crops in rows, seeding patterns and densities, and to a reduction in the use of tarpaulins that robots may find difficult to navigate. Pruning, leaf removal or foliage geometry could be reconsidered to improve the vision/recognition capacity of the robots by limiting, for example, the effects of occlusion by the leaves. Existing infrastructures in the plots (antennas, cables, fences, anti-hail nets, tree bagging, etc.) could be used to facilitate robot navigation or create new means of movement (suspended robots, poles with fixed structures above the plots for camera movement, movement of robots under photovoltaic panels with supporting structures, etc.) or more simply to carry visual or RFID signage to help the robot move. These structures could also be used to bring inputs (seedlings, fertilisers, etc.) directly to the agricultural plots so that small robots can retrieve them for their action in the field.
In animal production, milking robots are fixed robots inside the barn. With the current spatial organisation of the fields around the barns, dairy farms spend a large part of their time in stalls. In order to switch to a mainly grass-fed dairy system, one could imagine reorganising the farms, with for example fields arranged in a star shape around the barn containing the robot. Or one could imagine a milking robot that could be installed directly outside. Experiments at the Trévarez farm in France show, for example, a mobile milking robot placed at the junction between two separate grazing areas – one for daytime and one for night-time. By changing grazing areas in the morning and evening, the cows have to pass through the remote milking parlour in the field.
Agro-ecological practices require a high level of frequency and precision in both farming practices and in the number of passages made, which robots could help to meet. The use of robots with very precise geo-positioning systems could make it possible to redesign agricultural itineraries in the sense that the robots would have in memory the exact positions of all the seeds sown (and therefore no longer need an on-board vision system) and thus carry out extremely fine mechanical actions such as hoeing crops in all directions in space. This high positioning precision also makes it possible to envisage sowing patterns that are totally different from those currently used (grid, rhombus, etc.) and to integrate a whole complexity of companion plants, plant diversity and different phenological stages that are mapped very precisely as soon as they are sown, and followed throughout the crop cycle. One could then imagine having plants at various phenological stages within the same plot, each of which could be considered and taken into account to lead to dedicated actions. Given their complexity, agro-ecological systems will be increasingly difficult to observe and control as a whole. The division of elementary actions (sowing, weeding, harvesting, etc.) by robots – in swarms or not – with a dynamic mapping of the plot in mind could be made available for specific and precise tasks: weeding an area to transplant a seedling, removing senescent or diseased organs from a plant, or harvesting what is ripe. The division of elementary tasks is also interesting in the sense that it is not blocking if one of the systems fails and there is only a part of the itinerary to intervene on. By thinking about robotics in a way that is completely intertwined with other technologies or innovative systems, the robotic units make it possible to consider heterogeneities and diversity (of companion plants, cover crops, varieties, phenological stages, etc.). But keep in mind that we are not there yet…
Energy and environmental issues still too little considered
What about the energy autonomy of robots?
Even if some people are still reluctant to accept it, agriculture as it is currently practised could only come about with abundant energy, almost exclusively of fossil origin. The sector is absolutely dependent on it. With the Paris agreements that France has committed to respect, and through its national low-carbon strategy (SNBC), the challenge is to decarbonise the French energy mix, and consequently that of the agricultural sector. Let’s remember that in France, the agricultural sector represents only a few points of GDP (that’s another problem…) for about 20% of greenhouse gas emissions on the territory. If we put aside methane emissions that are fairly proportional to the size of the ruminant herd and nitrous oxide linked to mineral nitrogen fertilisation, the reduction of incoming carbon will be achieved by decarbonising agricultural traction. With the race for gigantism and the enormous on-board power of agricultural machinery, diesel engines have so far had a good run.
It is difficult to see clearly whether the size of robotic agricultural machinery will follow a downward trend compared with their conventional cousins. The argument of reduced soil compaction – a direct consequence of the lighter weight of robots – is constantly being put forward. Some robotics research work goes quite far in this direction and seeks to measure and analyse the influence of less soil compaction on the state of the ground, and to estimate the rolling parameters of the robot in activity (deformation measurements, load evaluation, sensors on the tyres, etc.). If we place ourselves in a logic of reducing the size of robots, we cannot ignore the question of the power embarked on these robotic machines – necessarily lower when the size of the robot decreases – for the management of agricultural activities. For surveillance or tours of the plain, it is reasonable to consider that the robots will use little energy. On the other hand, some practices, such as tillage, require a lot of pulling power, especially when the tillage is deep and the tools to be pulled are heavy. One way out of this could be to combine small robots in a swarm, each with a basic task to perform, or to try to combine or associate robots with each other to gain access to more available power and to transport and tow heavy implements.
The issue of energy in a robotic farm site has not yet been fully resolved. While many robots are powered by electric energy (wired electric, battery electric, on-board solar panel) – especially when it is produced by so-called “decarbonised” energy vectors – some of them are still powered by thermal and/or hybrid engines (Figure 10). The issues surrounding energy are all the more important as the limitation of energy capacities is an obstacle to the use of robotic machines on agricultural plots. There are many reasons for this. The work rates of the tools are quite low, which means that they have to be able to work for quite a long time. The environmental impacts can be potentially higher (especially if the robot has to be transported between the plots and the charging points if the robot is battery powered). Robots have to carry out interventions with delicate and targeted actions, which are not compatible with short and easily scheduled work sites

Figure 10. Overview of robots by energy vector. CAUTION: the information is not always correctly filled in by the manufacturers. Source: Directory of digital tools for farmers Translation from top to bottom : Hydrogène (hydrogen), Hybride (Hybrid), Solaire et Batterie (Battery and Solar), Thermique (Thermal), Electrique filaire (Wired electric), Non renseigné (Not filled), Electrique du Batterie (Battery operated electric)
The challenge of electrifying robots necessarily raises questions about their autonomy and also requires us to think about our capacity to produce this electricity. The batteries on electrified robots need to be recharged (as on conventional electric vehicles), which means that the robot has to be brought back to a recharging point, especially if the plots are far from the main farm. And the heavier the robots, the more powerful the batteries will need to be and the longer they will take to recharge, potentially further limiting the robots’ autonomy in their activities. Note that some will manage this constraint with hybrid robots. Others will prefer to install battery packs on the robots to avoid having to handle them regularly.
Current robots have to carry far too many functions and raw materials (sowing, fertiliser, etc.) to be completely autonomous in agricultural plots. The supply of electrical energy on the plots of use is thus in the line of sight of the players in the sector. One of the first topics of interest is charging stations. The idea here is to bring the material and energy directly to the point of use (in the plot) rather than imagining having a robot that is 100% autonomous throughout its activities. Can we set up a recharging station in the plots and thus reduce the number of return trips by the robot? Could several neighbouring producers use the same terminal? How could these charging stations (and the robots’ batteries) be powered: by small wind power stations on the farm, by solar installations directly on the plots, by methanisation units, using hydrogen technologies? The answers are not obvious and depend on the climatic conditions of the farm, its production objectives and constraints, or the context in which the energy produced is used. I refer you to a previous dossier on agrivoltaism.
In France, the electricity distribution network manager “Enedis” recently joined the Robagri association – a sign that the issue also seems to interest players that we might not have expected to see here. It would seem that 80% of agricultural plots are located less than 1 km from the Enedis network and that it would therefore be possible to take advantage of high-voltage lines to set up remote recharging stations in the fields. Some could take advantage of these stations to integrate communication infrastructures of varying speeds and support robotic operations (recognition and vision of the robot, detection of obstacles, control of the robot and associated tools, communication with a robot supervisor in the event of problems or dangerous situations, feedback of robot operating data, etc.). These charging stations could also be secure places for the robot when it is not in operation.
In the continuity of the charging stations, one could also imagine using the existing infrastructures in the plots (cables, poles, wires, posts, fences, etc.) to bring electrical energy to the robots (and/or to allow them to move on them as we discussed above), but also to make raw materials available (seed, fertiliser, etc.) in order to limit, for example, the load of the tanks (and consequently the need for energy) transported by the robots. Electricity supply networks could be installed in parallel with the existing irrigation networks. One interviewee told me about a start-up project with a robot on a watering system that uses the energy of the hydraulic system to move.
Unsurprisingly, the choice of electrification will have to be made with full knowledge of the risks of sourcing critical materials and minerals, particularly for the development of batteries. We already know, for example, that there would be major problems with the supply of elements such as lithium if the entire population adopted an electric vehicle. Even if the orders of magnitude are not the same in the agricultural context alone, the resilience of the agricultural model to supply shocks cannot be overlooked. Some robotic operators will have chosen to separate the purchase of the robot and the rental of the batteries, a way for them to better manage their stocks and ensure a longer battery life.
Current robots cannot operate 24 hours a day and there does not seem to have been any real reflection and work on the necessary autonomy of a robot according to its agricultural activity. Energy is perhaps still not expensive enough – even if the Russian-Ukrainian conflict has caused prices to rise sharply and required certain states to deploy tariff shields. Nevertheless, it seems necessary to place ourselves in situations of very high energy prices to test the resilience of the robotic agricultural models that may be proposed.
Life Cycle Assessment (LCA) of agricultural robotic systems
Although robotics tend to be promoted as a tool to support the ecological transition of the agricultural sector, it is clear that at the time of writing, almost no environmental impact assessment or life cycle assessment (LCA) has been presented on agricultural robotics. I would like to stress here that the focus should not only be on the life cycle analysis of the robot as such, but also on the life cycle analysis of the robot within an agricultural system.
After reading the previous sections, you should now be aware that agricultural robotics raises many environmental issues:
- Single-task agricultural robots are ultimately used for very little time during the entire crop cycle and spend most of their time in a shed. I would have heard in my interviews that conventional tractors are used at a rate of 10% (ratio of time spent in the field to time spent in the shed) compared to a rate of 2-3% for highly specialised robots. The tractor is effectively used for several farming operations and its impact can then be allocated to several work cycles or smoothed over the whole production. In this context, the sale of single robots raises questions in the sense that an economy of functionality (selling a weeding service rather than a weeding robot) or the mutual purchase of robots (within a Cooperative union for agricultural equipment for example) could raise the low rates of use of robotic tools.
- the batteries of electrified robots will have to be manufactured and recycled at the end of their use (and we know how complex this recycling stage is)
- agricultural robots, according to current regulations, must be moved and transported on agricultural plots, which directly generates impacts due to the use of a transporter
- many of the current robots are still in the development or testing stage and need to be repaired more regularly.
Life cycle assessment (LCA) work on robotics is still in its infancy. A recent study sought to compare conventional weeding practices in viticulture (between the rows and under the rows) with those of robotic mechanical weeding in some major French terroirs (Pradel et al., 2022). Even in this relatively small case study, the work is far from obvious. Measuring the impact of agricultural robotics requires being able to measure impacts from both an agronomic and environmental point of view, and there are currently no metrics capable of quantifying and objectifying these elements. Rather than working in absolute terms, one solution could be to define reference cropping itineraries and compare robotic systems with conventional systems. However, it is necessary to be able to characterise these references precisely and, above all, to be able to choose them. Should we compare ourselves to a conventional system? Should we compare ourselves to a system with innovative agronomic practices? How can a reference be chosen when the conventional itineraries used vary by territory, as is the case for vine weed control, for example? Compromises also need to be made in terms of robot size and autonomy in the sense that a fleet of robots could be less interesting from an LCA point of view if they have to be transported regularly and if energy autonomy in the field cannot be guaranteed. The logistical flows of transporting machines and operators, and the autonomy of field operations seem to be the areas of work identified to date for limiting the carbon footprint (and not the full life cycle assessment) of robotic systems. The transport of operators is also considered here in the sense that regular repair needs will require operators to travel to the field.
The difficulty of these analyses also lies in the fact that the current databases for carrying out life cycle analyses are not consolidated enough. In Agribalyse, for example – the reference database on agricultural topics – current agricultural machinery is still simply considered as scrap metal and steel, whereas the on-board electronics can no longer really be neglected (just look at the quantity of cables and consoles that there can be in a tractor cab). And when we start to look at the carbon footprint of the digital tools potentially installed on machines – and robots are for the most part loaded with sensors – the stick starts to hurt because the digital emission factors are missing. In addition to their own life cycle, most of these digital technologies will make it possible to collect a whole host of data (machine operation, state of the plant biomass, health quality of a plot of land, etc.), the quantity of which is far from negligible. By following the collection of data on an Italian plot of land for 15 years and by doing a bit of forecasting, a recent article by Kayad et al. (2022) estimated, for example, that 40 Gigabytes (GB) of data would be collected per hectare in 2025 using digital tools. Keep in mind that this parcel was monitored for research purposes and therefore naturally the authors had collected quite a lot of data (and that in my humble opinion, on closer inspection, some data – particularly satellite data – may have been underestimated). Nevertheless, the authors show sharp breaks in the amount of data stored with the advent of certain data acquisition technologies (notably drones).
Scouting robots are likely to collect absolutely gigantic quantities of data. Here again, there are storage issues, but also and above all communication issues. With on-board vision technologies, we can expect robots to collect thousands of images per hectare. At resolutions of a few megabytes per image, the bill is immediately quite high and it is thus possible to collect several gigabytes of data per hectare (and this for just one type of surveillance). As communication infrastructures are not strong enough in the agricultural context (good luck with 5G on farms), the challenge will be to be able to embed the processing directly on the machine (this is called ‘edge computing’ compared with ‘cloud computing’ carried out on servers outside the robot) so that only the results of the processing – which is much lighter in IT terms (e.g. the presence or absence of a disease, an estimate of yield, etc.) – can be kept and the images acquired can be discarded so that they do not have to be transferred as well. And these edge computing devices will necessarily have to be powerful and economical insofar as it will not be possible to put computing infrastructures costing several thousand euros on a robotised agricultural machine. Of course, there will still be energy issues if we imagine frugal autonomous machines, since high-performance calculations are particularly energy-intensive.
For the time being, life cycle analysis is still too much like a new criterion for evaluating robots, whereas it should be the key to entry, a sort of framework that would constrain current robotics developments. The robotics sector is still young, and without acculturation on the issues of energy and environmental transition, there is a great risk that robots will get bogged down and will only be able to go backwards with great difficulty.
What kind of vision and model of society do we want?
We have talked several times about co-evolution between humans and machines, but it will also be fundamental to bring together different working disciplines and different actors in society. At present, the predominance of engineering researchers in the robotics field – who know very little about the agricultural world – has mainly led to the development of robotic units integrated into the current agricultural model and designed to perform exactly the same tasks as humans. Agronomists and roboticists need to work together to ensure that the proposed robots are not simply designed for automation, but that they are positioned in a quality agricultural model. Agronomists and ecologists will certainly have to focus on agricultural and environmental production, but not forget the operational dimensions of agricultural activities (labour time, implementation constraints, etc.). It will be necessary to be able to converge in the field, and the results and deliverables will necessarily be more realistic than what is in the heads of the roboticists on one side or the agronomists on the other. Some robots are imperfect, and that’s a fact, but the first grape harvesters and combines were a disaster when they started, before co-evolving into something more operational.
I emphasise here that the presence of robotic systems in an agricultural context should not be imagined in a binary assertion. The approaches to digitisation and robotisation are extremely numerous and everyone will find something to suit them. There is a huge gradient between a fully automated and robotised farm and a farm that has chosen to turn away from these tools entirely, with areas where digital and robotic tools will accompany agricultural choices and itineraries and where a great deal of freedom of choice will still be left. And one might even wonder whether farmers would be prepared to supervise remote robots even if they could. It is still difficult today to assess the spectrum of imaginings, as there are so many possibilities for the evolution of the sector. It is possible, for example, that pesticide application will increase as application costs decrease, or that more powerful – and perhaps dangerous – pesticides will be used once spraying tasks have been dedicated to robots.
Insofar as agricultural robots can both open the way to an ecological utopia and reinforce the dominant industrial model (I invite you to re-read the section on the fractures and risks opened up by agricultural robotics), We must make sure that as many stakeholders as possible are brought to the table so that the future of robots is not simply decided by a handful of manufacturers and farmers, but by society as a whole (I had already discussed the concept of innovation and responsible research – RRI – in a previous blog entry). The articulation between agriculture and technology will have to be tackled head on, especially as the time horizons are extremely varied between changes in consumer demand, development cycles or regulatory times. Whether or not to move towards robotics will impose societal choices and farm models (changing practices, stopping certain crops, adapting farms to robotics or not, etc.). For example, should we accept the development of pollination robots? When we know that millions of years of evolution have made it possible to improve pollination by plants and insects, should we really try to replace nature and turn to transhumanism? Robotics could push us to accept extreme situations that we do not want. Agriculture is indeed still a playground for some industrialists and we must jointly decide at what point automation or industrialisation should stop. If robots are currently able to almost fully automate the construction of vehicles, could we expect robotic units to be able to make ham?
As we have discussed, robotics is increasingly being developed in greenhouses (leafy vegetables, fruit vegetables, seeds…), for fairly obvious reasons of ease of implementation (ease of navigation, standardised production…). Although greenhouses (horizontal, vertical, container…) raise questions in terms of energy, these formats are still widely promoted in the traditional media. I would remind you that urban agriculture has no reason to feed the planet. The example of the current population of Paris, which needs a 150 to 300km belt to feed itself, is a rather good example. However, this is not a reason to oppose head-on these agricultural systems – sometimes highly robotised – which can be an opportunity to meet niche demands (in fruit, for particular population profiles), to reclaim lost urban spaces, or simply to re-focus the population on agricultural production. Some robotic greenhouse systems have gone a long way in thinking about their agricultural system by seeking to limit the drudgery of agricultural operators by means of an overhead crane moving robotic tools while keeping agricultural production in the ground.
Towards the acceptability of robots in the agricultural context?
Will robotic agricultural machines be widely accepted by the population if they start to be democratised? What would be the impact of a “robot-free agricultural product” label? What image would a completely autonomously produced organic milk have? What place would be given to milk produced in a neighbouring country by hand compared to milk produced nearby using robotic units? All these questions are actually more societal and political than technological. They echo the reflections on the agricultural model towards which we wish to converge, but also the representation that the population has of the agricultural world. Robotics will have difficulty becoming part of the mainstream if its only messages revolve around saving labour. There will be a need to change the scope of thinking if the sector wants consumers to want these robots to see the light of day, with, for example, specific specifications to emphasise the reduction of chemical treatments
The arrival of a new technological tool is always disruptive and its adoption generally follows a process of co-evolution in the sense that both man and tool adapt to converge towards the most appropriate use. When the first tractors were introduced into agriculture, it was relatively difficult to imagine what they could be used for. Farmers tended to use them in a similar way to their horses. Some farmers will never have been able to accept or switch to using tractors anyway (and there is absolutely nothing wrong with that – there are multiple trajectories of mechanisation) but others will have been able to co-evolve with the machine to apply it to uses they would never have thought of before.
Autonomous robotic machines, if they emerge, will follow the same long process of adoption. First, a relationship of trust will have to be built between the farmer and the manufacturers to ensure that the tasks performed by the robot are as good as if they had done them themselves. Manufacturers may propose a gradual evolution in the use of robots, starting for example by electrifying tractors, making tractors autonomous by allowing the farmer to take control, or deploying fleets of robots with a varying level of autonomy from a lead tractor or robot directed by the farmer for example. Some roboticists will try not to introduce too strong a technological breakthrough (e.g. by keeping classical attachment systems for tool carriers) so that farmers get used to robotic systems in their current context before opening up spaces for creativity around robots. These progressive approaches will facilitate the appropriation of robotic tools and allow the farmer to see how the robots could be integrated into his cropping itineraries and co-evolve with them. Autonomous driving will perhaps take the longest to be accepted in the sense that driving a tractor is still very much part of the farming mentality. On mechanised (but not autonomous) machines with very precise GNSS positioning navigation, once the hitched implements are well set up and coupled, the operator is essentially present to make U-turns and the added value of this human presence, especially if it is a farmer, is fairly limited. If we talk about cost now, the farmer may not be counting his hours, but it will not be the same for an employee. Autonomous driving may, however, be an opportunity to leave routine activities behind and to be active in other activities (going to the general assembly of one’s cooperative, doing sales, keeping an eye on agronomy, etc.) or to rethink the organisation of agricultural work by leaving much more room for observation of the field, agronomy and understanding of living phenomena.
In France, the 2021 agricultural census showed that the number of farms (currently around 390,000) has continued to decline over the last decade, albeit at a slower rate than in previous decades. While this decline may be surprising and even legitimately worrying, in the end very few farms disappear (and those that do are not necessarily the smallest) and are mainly bought out. Medium-sized farms are growing, but the largest structures are not growing on average. The expansion of farms goes hand in hand with the professionalisation of the sector, which must be increasingly technical (management of weed resistance without chemicals, management of the collapse of soil fertility, etc.) and respond to the ever greater demands of society. To be a little piquant, one might also wonder whether, in France, it is not by wanting to maintain family structures in agriculture that we have encouraged (directly or indirectly) the deployment of robotic tools. For example, as we have discussed in this dossier, the very large dairy farms in certain industrialised countries are not equipped with milking robots but rather with rotolactors.
In any case, there can be no change in production systems if society as a whole does not change. Our production and consumption patterns are leading us straight into the wall. Fortunately, the Ministry of Agriculture recently changed its name to the Ministry of Agriculture and Food Sovereignty… The speed of climate change is unsustainable – and largely linked to our production and consumption patterns, and these emissions are increasing linearly with the search for economies of scale. Technology has a share of the responsibility, but it should not be held responsible for everything. Even if the digitisation and robotisation of certain aspects of our activities could scare many away (over-equipping farmers who are already in debt, negative image of the sector, loss of jobs in the sector, etc.), we must nevertheless be wary of excessive demonisation and assume our societal choices. In our current globalized ecosystem, the refusal of robotization could require us to relocate certain productions or, on the contrary, to increase our financial contribution to the agricultural sector by strongly supporting the installation of well-paid young people and by significantly increasing the part of our budget allocated to food. If we are not ready for this, the trend will remain to reduce mechanisation costs and to reduce the wage bill on farms (at €20 per hour for driving a tractor, the choice of a robot to reduce direct costs makes sense), observations to which current agricultural robotics can respond.
As a conclusion
Robotic systems have been widely developed in agriculture, this is a reality. However, while the range of robotic systems is extremely wide, there are still relatively few robotic units on farms. The vast majority of robots are integrated into livestock farms – mainly on dairy farms with milking robots – because the more structured working environments facilitate their implementation. Robots in crop production are very numerous in the panorama, but still very little available in the field. It is clear that the positioning of robotics players in the agricultural sector is still rather vague and that each one seems to be looking for its place. Moreover, it is not clear whether the robots on offer are actually functional, whether they are being tested, or whether they are in full development.
Despite all the hype about autonomy in agricultural robotics, no robot is really 100% autonomous because an operator must always be there to move it around a plot of land or accompany it during its agricultural activities. Many scientific studies have been able to find scenarios in which autonomous operations or operations in collaboration with a human are profitable, but this does not mean that autonomous equipment or robots will be developed for these situations as some markets are too small to cover the development costs.
The introduction of robots in an agricultural context is still an open question that has not been resolved. The dimensions to be considered are extremely broad and cannot be reduced to simple binary positions, especially as the trajectories of digitalisation and robotisation in farms are extremely varied. The challenge will be to bring many players to the table (public, private, citizens, etc.) to decide together on desirable agricultural models and the link between agriculture and technology.
Soutenez Agriculture et numérique – Blog Aspexit sur TipeeeBibliography complementary to the interviews
Basu, S. et al. (2020). Legal framework for small autonomous agricultural robots. AI & Society, vol 35:113-134
Daum, T. (2021). Farm robots : ecological utopia or dystopia ? Trends in Ecology & Evolution, vol 20
Ditzler, L. & Driessen, C. (2022). Automating Agroecology: How to Design a Farming Robot Without a Monocultural Mindset? Journal of Agricultural and Environmental Ethics, vol 35: 2
Driessen, C. & Heutinck (2014). Cows desiring to be milked? Milking robots and the co-evolution of ethics and technology on Dutch dairy farms. Agricultural Human Values. 18p
EU Robotics (2021). European Robotics in agri-food Production. Opportunities and Challenges
GIS Relance Agronomique (2018). Demain l’Agriculture. Concours de Nouvelles. Educagri Editions.
FAO (2020). Agriculture 4.0. Agricultural robotics and automated equipment for sustainable crop production. Integrated Crop Management, vol 24
Kayad et al. (2022). How many gigabytes per hectare are available in the digital agriculture era? A digitization footprint estimation. Computers and Electronics in Agriculture, 198
Lachia (2018). Usage des robots en agriculture. Observatoire des usages de l’agriculture numérique https://agrotic.org/observatoire/2018/10/09/usage-des-robots-en-agriculture/
Lenain et al. (2020). Agricultural robotics : part of the new deal. With 27 agricultural robot information sheets. FIRA 2020 Conclusions. Editions Quae
Lowenberg‑DeBoer, J. et al. (2019). Economics of robots and automation in field crop production. Precision Agriculture, vol 21: 278-299
Lowenberg‑DeBoer, J. et al. (2021). Economics of autonomous equipment for arable farms. Precision Agriculture, vol 22: 1992-2006
Lowenberg‑DeBoer, J. et al. (2021). Lessons to be learned in adoption of autonomous equipment for field crops. Applied Economy Perspective Policy, 1-17
Lowenberg‑DeBoer, J. et al. (2021). The impact of regulation on autonomous crop equipment in Europe. International Conference on Precision Agriculture. John V. Stafford (ed.)
Lytridis, C. et al. (2021). An Overview of Cooperative Robotics in Agriculture. Agronomy, vol 11
Marinoudi, V. et al. (2019). Robotics and labour in agriculture. A context Consideration. Biosystems Engineering, vol 184: 111-121
Martin, P. (2021). A Future-Focused View of the Regulation of Rural Technology. Agronomy, vol 11
Martin, T., et al. (2021). Diversité et spatialité de la France laitière par le prisme des entreprises du robot de traite. Journées de Recherches en Sciences Sociales (JRSS), INRAE; SFER; CIRAD,
Martin, T., et al. (2021). Robots and Transformations of Work on Farms: A Systematic Review. The 2nd International Symposium on Work in Agriculture
Oliveira, L.F.P. (2021). Advances in Agriculture Robotics: A State-of-the-Art Review and Challenges Ahead. Robotics, vol 10
Pearson, S. (2022). Robotics and Autonomous Systems for Net Zero Agriculture. Current Robotics Reports, vol 3:57-64
Pradel, M. et al. (2022). Comparative Life Cycle Assessment of intra-row and inter-row weeding practices using autonomous robot systems in French vineyards. Science of the Total Environnement, vol 838
Redhead, F., et al. (2015). Bringing the Farmer Perspective to Agricultural Robots. CHI 2015, Crossings, Seoul, Korea
Rose, D.C. et al. (2021). Responsible development of autonomous robotics in agriculture. Nature Food, Comment, vol 2
Shockley, J. (2021). How will regulation influence commercial viability of autonomous equipment in US
production agriculture? Applied Economy Perspective Policy, 1-14
Sparrow, R. & Howard, M. (2020). Robots in agriculture: prospects, impacts, ethics, and policy. Precision Agriculture
Vasconez, J.P. (2019). Human-Robot Interaction in Agriculture: a Survey and Current Challenges Biosystems Engineering, vol 179:35-48
Vik, J. et al. (2019). The political robot – The structural consequences of automated milking systems (AMS) in Norway. NJAS – Wageningen Journal of Life Sciences. 9p
Interviewees
Name | Structure |
Guillaume BOCQUET | AXEMA |
Jean-Pierre CHANET | INRAE |
Christian GERMAIN et Florian RANCON | Laboratoire IMS – Chaire AgroTIC |
Romain FAROUX | Consultant |
Amélie FISCHER et Clément ALLAIN | Idele |
Michael FONTANIN | Vitibot |
Jean-Albert FOUGEREUX | FNAMS |
Christian HUYGHE | INRAE |
Florentin KACAR | CTIFL |
Roland LENAIN | INRAE |
James LOWENBERG- DeBOER | Harper University |
Léo PICHON | Montpellier SupAgro – Chaire AgroTIC |
Xavier REBOUD | INRAE – Robagri |
Davide RIZZO | UniLaSalle – Robagri |
Cédric SEGUINEAU | Naïo Technologies |
Kévin TAMBOISE | Agriculteur |
Inès TEETAERT | Arvalis |
Bruno TISSEYRE | Montpellier SupAgro – Chaire AgroTIC |